
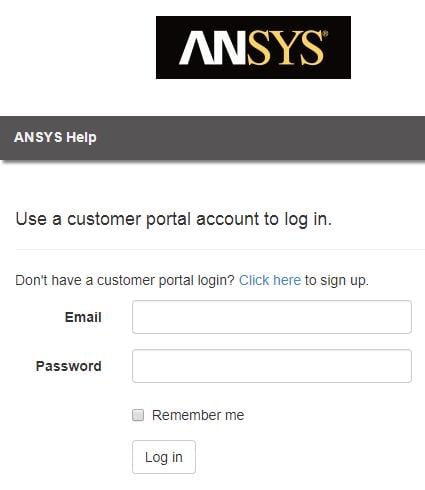
Ansys email software#
Now they can build the entire virtual prototype through software simulation and create an optimal design by exploring thousands of designs. In the past, engineers would build multiple prototypes in hardware, resulting in long times and cost. As a result, engineers no longer need to build and test several different configurations. Through digital modeling, engineers can vary the pressure and temperature of the valve to gauge its strength and discover failure points more quickly. A more specific example would be a valve in an aircraft engine that regulates pressure in a pipe, or a duct that needs to be modeled in many ways.

The best way to understand the advantages of simulation is by looking at an example: One blue chip customer is leveraging simulation technology to kickstart digital transformation initiatives that will benefit customers by lowering development costs, cutting down the time it takes to bring products to market. Companies use simulation software to design their products in the digital domain - on the computer - without the need for expensive and time-consuming physical prototyping. Prith Banerjee: Simulation and modeling help companies around the world develop the products that consumers rely on every day - from mobile devices to cars to airplanes and frankly everything in between. VentureBeat: What do executive managers need to know about modeling and simulation today? They both allow us to peer deeper into things, but how do these underlying technologies serve in various contexts to speed up the ability to explore different designs, trade-offs, and business hypotheses? A smaller value provides for easier convergence but with more penetration.This interview has been edited for clarity and brevity. If bending deformation dominates, use a smaller value (0.1).The default value of 1.0 is appropriate for bulk deformation.I typically go with about 0.1, especially when I run into convergence issues.Įnter the Normal Stiffness factor.
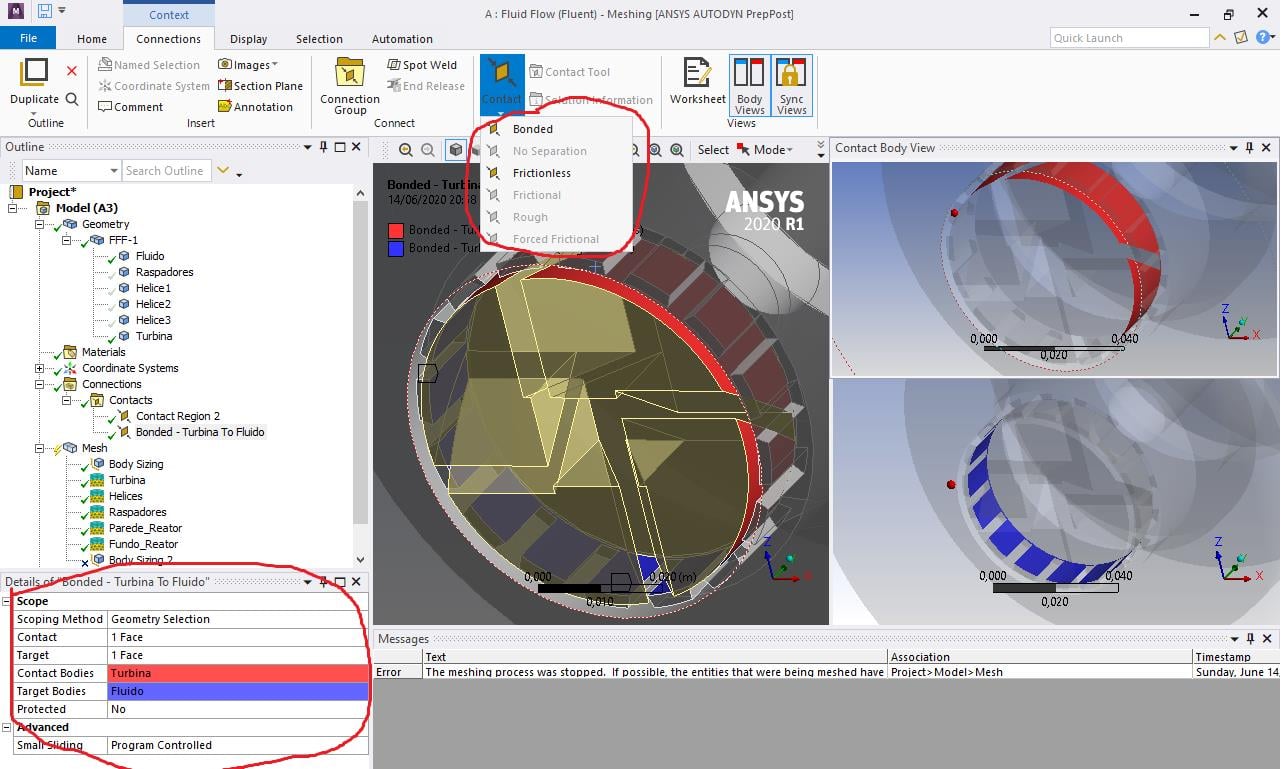
Ideally, you want a high enough normal stiffness that the penetration is acceptably small, but a low enough normal stiffness that the problem will be well-behaved in terms of convergence. Lower normal stiffness values can lead to a certain amount of penetration and produce an inaccurate solution. Higher normal stiffness values decrease the amount of penetration but can lead to ill-conditioning of the global stiffness matrix and to convergence difficulties. A value of 1 is usually appropriate.Ībout the normal stiffness factor, it primarily controls the amount of penetration between contact and target surfaces. The value of the stabilization damping factor should be large enough to prevent rigid body motion but small enough to ensure a solution. The damping is applied to each load step where the contact status is open. This contact damping factor is applied in the contact normal direction and it is valid only for frictionless, rough and frictional contacts. The stabilization damping factor provides a certain resistance to damp the relative motion between the contacting surfaces and prevents rigid body motion. The contact will not get detected during the analysis and can cause a rigid body motion of the bodies defined in the contact. This section is from the manual:Ī contact you define may initially have a near open status due to small gaps between the element meshes or between the integration points of the contact and target elements. Note that stabilization damping factor also helps with Rigid body motion. Their purpose is similar to weak springs and should be carefully monitored since they add artificial energy. Hi Jon, Yes Stabilization is like adding dampers to the springs, so it helps contain large displacements for small load increments.
